· Eduardo Vieira · Industrial Automation · 3 min read
Top 5 Industrial Automation Trends Transforming Manufacturing in 2025
Discover the cutting-edge technologies and approaches that are revolutionizing industrial automation and how they can benefit your manufacturing operations.
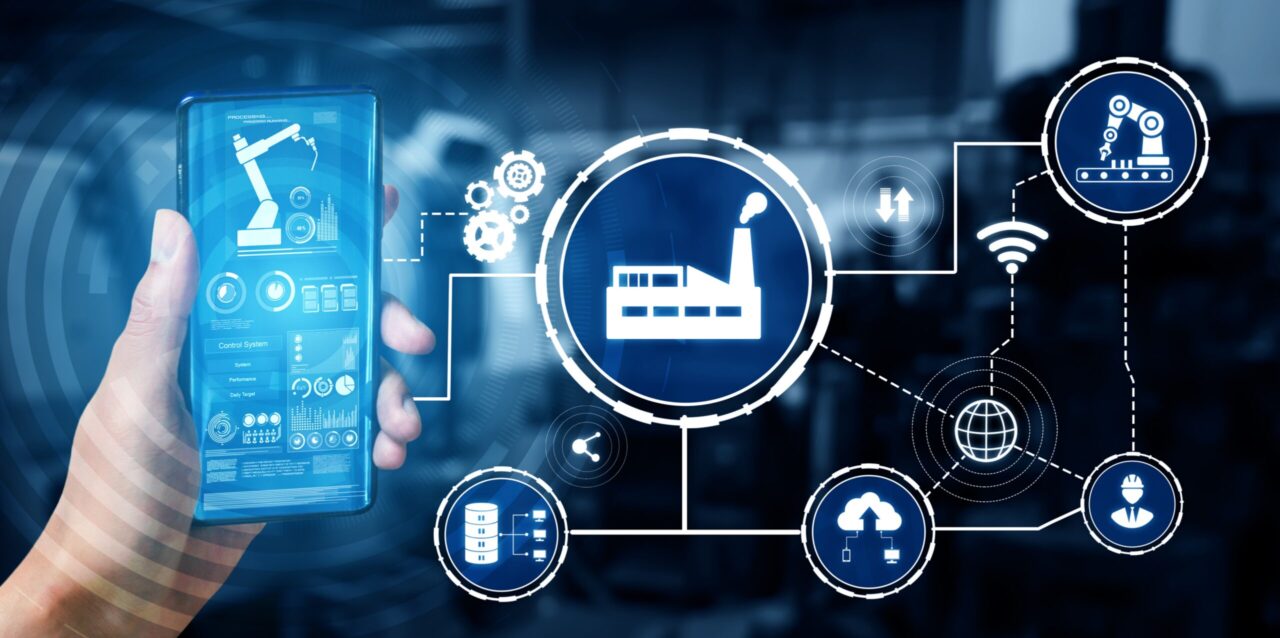
The industrial automation landscape is evolving at an unprecedented pace, driven by technological advancements and the increasing need for efficiency, flexibility, and resilience in manufacturing operations. As we move through 2025, several key trends are shaping the future of industrial automation and providing new opportunities for businesses to optimize their processes and gain competitive advantages.
1. Edge Computing in Industrial Environments
Edge computing has emerged as a game-changer in industrial automation, bringing computational power closer to where data is generated. This approach significantly reduces latency, enhances real-time decision-making capabilities, and decreases bandwidth usage.
Key Benefits:
- Real-time processing of critical data
- Reduced dependency on cloud connectivity
- Enhanced security for sensitive operational data
- Lower bandwidth costs and network traffic
2. AI-Powered Predictive Maintenance
Artificial Intelligence and Machine Learning are revolutionizing maintenance strategies in industrial settings. Predictive maintenance systems can now analyze patterns in equipment performance data to forecast potential failures before they occur.
Implementation Approaches:
- Sensor networks that monitor equipment vibration, temperature, and acoustics
- ML algorithms that identify anomalies and predict failure points
- Integration with maintenance management systems for automated scheduling
- Digital twins for simulating equipment behavior under various conditions
3. Collaborative Robots (Cobots)
Unlike traditional industrial robots that operate in isolation, collaborative robots are designed to work alongside human operators, combining human flexibility and problem-solving with robotic precision and endurance.
Emerging Applications:
- Quality inspection and testing
- Assembly of complex components
- Material handling in dynamic environments
- Hazardous task execution with human supervision
4. Industrial IoT (IIoT) Ecosystems
The Industrial Internet of Things continues to mature, creating interconnected ecosystems of machines, systems, and processes that generate valuable operational insights.
Key Developments:
- Standardization of communication protocols
- Enhanced cybersecurity frameworks for industrial systems
- Low-power, long-range connectivity options for remote monitoring
- Integration platforms that connect legacy equipment with modern systems
5. Web-Based HMI and Remote Monitoring
The shift toward web-based Human-Machine Interfaces (HMIs) and remote monitoring capabilities has accelerated, enabling operators and managers to access critical system information from anywhere.
Advantages:
- Platform-independent access to control systems
- Responsive interfaces that adapt to different devices
- Enhanced visualization of complex data through modern web technologies
- Secure remote troubleshooting and system adjustments
Conclusion
These trends represent significant opportunities for manufacturers to enhance their operations through strategic implementation of automation technologies. The key to success lies not just in adopting these technologies, but in implementing them thoughtfully with a clear understanding of specific operational needs and challenges.
As an automation engineer specializing in these areas, I’ve seen firsthand how the right combination of these technologies, properly implemented, can transform manufacturing operations and deliver substantial returns on investment. The most successful implementations start with a thorough assessment of current processes, clear identification of pain points, and a strategic roadmap for technology adoption that aligns with business objectives.
If you’re considering how these trends might benefit your manufacturing operations, I’d be happy to discuss your specific challenges and opportunities. Contact me to explore how these emerging technologies can be applied to your unique situation.