· Eduardo Vieira · Mechanical Engineering · 7 min read
Mechanical Design for Industrial Automation - Bridging Physical and Digital Systems
Discover how mechanical engineering principles must evolve to support modern industrial automation, creating designs that integrate seamlessly with sensors, actuators, and control systems.
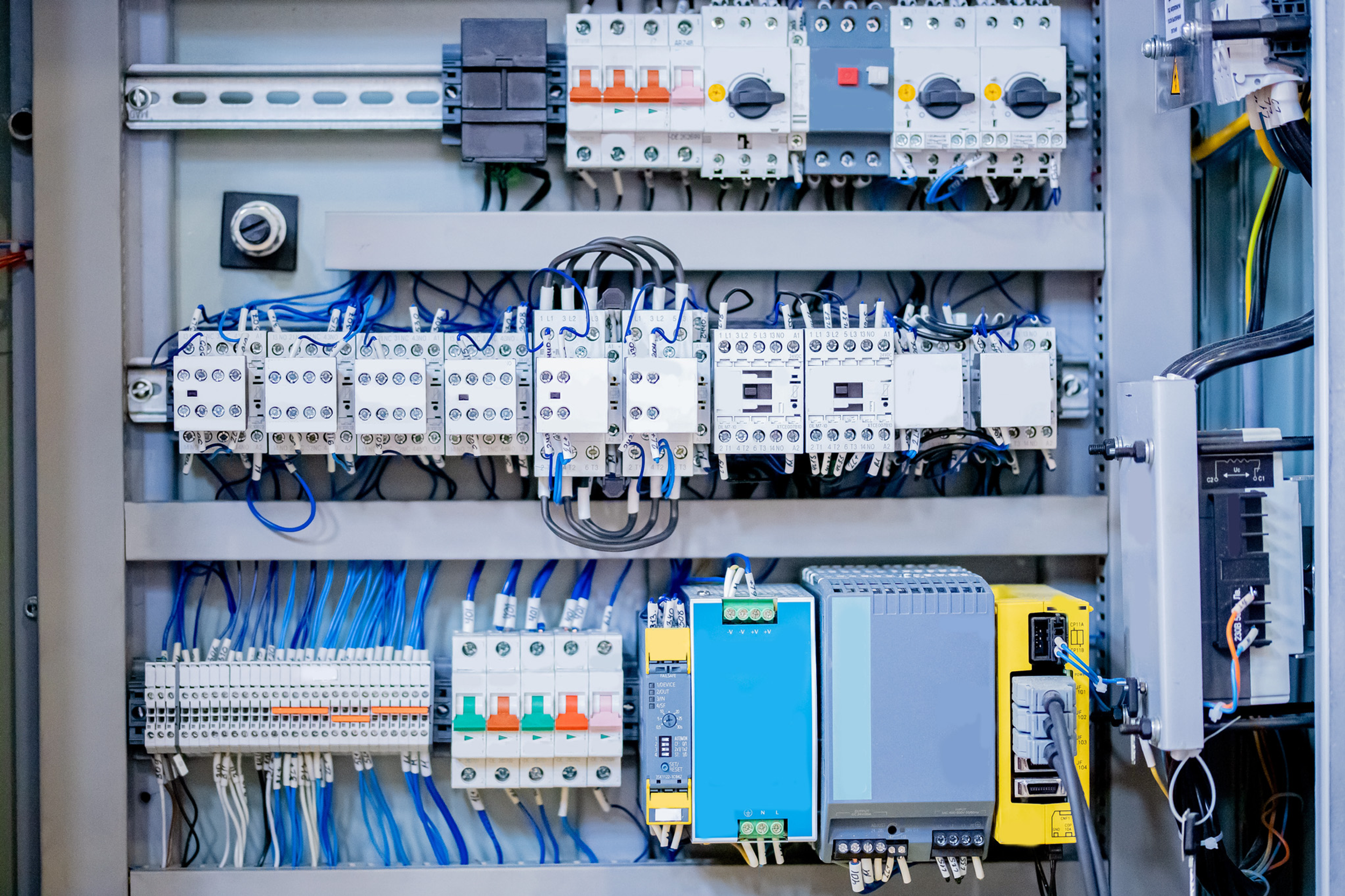
Mechanical Design for Industrial Automation: Bridging Physical and Digital Systems
Modern industrial automation systems represent a convergence of mechanical engineering, electronics, and software. As automation becomes increasingly sophisticated, mechanical design must evolve beyond traditional considerations to accommodate sensors, actuators, controllers, and communications infrastructure. The most successful industrial systems are those where mechanical design and automation systems are developed in concert, with each supporting the other.
Drawing from my dual expertise in mechanical engineering and industrial automation, I’ve developed a comprehensive approach to mechanical design that anticipates automation requirements while maintaining core mechanical engineering principles. This article explores key considerations, best practices, and real-world case studies of successful integration.
The Evolution of Mechanical Design for Automation
Traditional mechanical design focused primarily on static and dynamic loads, material properties, manufacturability, and maintenance. While these considerations remain essential, mechanical designs for automated systems must also address:
- Sensor integration: Providing appropriate mounting locations and access for various sensors
- Actuator accommodation: Designing mechanical systems that can be effectively controlled by motors, pneumatics, or hydraulics
- Cable and conduit pathways: Creating routes for the extensive wiring required by modern control systems
- Control panel space: Allocating appropriate space for control hardware
- Data collection points: Enabling monitoring of critical parameters
- Human-machine interfaces: Integrating operator controls and displays
Case Study: Redesigning a Manual Production Line for Automation
A food packaging company needed to automate a previously manual packaging line. Initial automation attempts failed largely due to mechanical designs that hadn’t considered automation requirements.
Original Mechanical Design Issues:
- Inconsistent product positioning made sensor detection unreliable
- Vibration from mechanical systems triggered false sensor readings
- Insufficient space for control components
- No defined pathways for wiring and pneumatic lines
- Poor access for maintenance of electrical components
Integrated Redesign Approach: Working with the client, I developed a new mechanical design specifically optimized for automation. Key elements included:
- Precision guide rails ensuring consistent product positioning
- Vibration isolation for sensitive detection areas
- Dedicated control enclosure space integrated into the frame design
- Pre-defined cable trays and pneumatic line pathways
- Modular components designed for easy access and maintenance
- Standardized mounting patterns for sensors and actuators
Results:
- Reduction in false sensor triggers
- Reduction in installation time
- Reduction in wiring costs
- Improvement in maintenance accessibility
- Successful automation achieving higher throughput of manual operation
Key Principles for Automation-Friendly Mechanical Design
1. Design for Consistent Positioning and Registration
Automation systems require consistent, repeatable positioning to function reliably:
- Implement positive stops for workpieces and moving components
- Use kinematic constraints to ensure parts self-locate in the same position every time
- Incorporate alignment features that force proper assembly
- Design fixtures that present consistent interfaces to sensors and tooling
- Control tolerances tightly in areas critical to sensor performance
Practical Example: For a medical device assembly process, I replaced a traditional V-groove component guide with a precision linear rail system and tooling plate with dowel-pin locating features. This reduced position variability, enabling reliable vision system inspections that were previously impossible.
2. Account for Sensor Requirements Early in Design
Different sensor types have specific mounting and environmental requirements:
- Photoelectric sensors need unobstructed line-of-sight and protection from ambient light
- Proximity sensors require specific mounting distances and target materials
- Vision systems need consistent lighting and backgrounds
- Temperature sensors need thermal isolation from heat sources/sinks that could affect readings
- Vibration/acoustic sensors need isolation from unrelated vibration sources
Practical Example: When redesigning a metal stamping inspection station, I incorporated dedicated mounting brackets with micro-adjustment capabilities for photoelectric sensors, surrounding them with shrouds to prevent interference from ambient light. This increased detection reliability.
3. Plan for Control System Infrastructure
Control systems require significant infrastructure that must be accommodated in mechanical designs:
- Reserve space for control panels, junction boxes, and network infrastructure
- Design in cable channels and conduits with sufficient capacity for future expansion
- Consider heat dissipation from drives and power supplies
- Provide service access to all electronic components
- Incorporate grounding points for electrical safety and EMI reduction
Practical Example: For a large packaging machine, I designed a modular frame system with integrated cable trays and dedicated control cabinet mounting zones. This approach reduced wiring time and made future modifications significantly easier compared to previous designs that treated control system infrastructure as an afterthought.
4. Design for Motion Control
Automated systems often incorporate sophisticated motion control that imposes specific mechanical requirements:
- Minimize backlash in drive systems for precise positioning
- Account for servo tuning by designing systems with consistent friction and inertia
- Consider dynamic forces from acceleration and deceleration
- Implement proper support for linear motion systems to prevent binding
- Design appropriate hard stops and limit switches to prevent overtravel
Practical Example: When automating a precision assembly process, I replaced a traditional lead screw motion system with a rigid ball screw assembly, coupled with an oversized servo motor. The mechanical redesign allowed the system to achieve better positioning accuracy while moving at higher speeds than the previous system.
5. Consider Maintenance and Serviceability
Automation components require regular maintenance and occasional replacement:
- Design for modular replacement of both mechanical and electrical components
- Provide adequate access to maintenance points without major disassembly
- Use quick-disconnect fittings for pneumatic and electrical connections
- Label service points directly on the machine structure where possible
- Create dedicated access panels for components requiring frequent attention
Practical Example: For a food processing line, I redesigned the conveyor system with hinged access panels and quick-release belt mechanisms. This reduced routine cleaning time and conveyor belt replacement time.
6. Implement Standards and Modularity
Standardized, modular designs significantly improve both implementation and long-term operation:
- Develop standard mounting patterns for sensors, actuators, and control components
- Use consistent fastener types and sizes throughout the design
- Create modular subsystems that can be pre-assembled and tested
- Implement industry standard interfaces rather than custom connections
- Maintain consistent design language across similar components
Practical Example: For a client with multiple production lines, I developed a standard mechanical interface specification for all equipment. This allowed them to standardize sensor types, spare parts inventory, and maintenance procedures across different machines, reducing training requirements and maintenance costs.
Integration Tools and Methodologies
Modern design tools facilitate the integration of mechanical design and automation systems:
CAD Integration with Electrical Design
Advanced CAD systems now support:
- Electrical schematic integration with 3D models
- Automated cable routing and length calculation
- Panel layout optimization
- Collision detection for moving components
Digital Twins for System Validation
Digital twin technology enables:
- Simulation of mechanical systems with control logic
- Virtual commissioning before physical construction
- Testing of fault conditions safely
- Operator training using accurate system models
Mechatronic Design Process
The most effective approach integrates:
- Concurrent development of mechanical, electrical, and control systems
- Regular cross-disciplinary design reviews
- Simulation of integrated systems before finalization
- Prototype testing with actual control components
- Iterative refinement based on system-level performance
Future Trends in Mechanical Design for Automation
Several emerging trends are shaping the future of mechanical design for automation:
1. Designed-in IoT Capabilities
Modern mechanical designs increasingly incorporate:
- Embedded sensor mounting points throughout the structure
- QR codes or RFID tags for component identification and tracking
- Data collection points for predictive maintenance
- Modular upgrade paths for future connectivity
2. Adaptive and Reconfigurable Systems
Next-generation automation requires:
- Quickly reconfigurable mechanical interfaces
- Tool-less adjustment for different product variants
- Standardized connection points for auxiliary equipment
- Mechanical systems that support flexible manufacturing concepts
3. Human-Robot Collaboration Spaces
As collaborative robots become common, mechanical designs must accommodate:
- Elimination of pinch points and hazards
- Dedicated collaborative work zones
- Appropriate safety sensors and guards
- Intuitive human interfaces
Conclusion
Effective mechanical design for industrial automation requires a holistic approach that considers both traditional mechanical engineering principles and the unique requirements of modern control systems. By addressing sensor integration, control infrastructure, motion requirements, maintenance access, and modularity early in the design process, engineers can create systems that are not only mechanically sound but also optimized for automation.
The most successful automated systems result from close collaboration between mechanical engineers and automation specialists, with each discipline informing and enhancing the other. This integrated approach delivers systems that are more reliable, easier to implement, and less costly to maintain throughout their operational life.
As both a mechanical engineer and automation specialist, I’ve found that bridging these disciplines creates opportunities for innovation and performance improvements that aren’t possible when treating them as separate domains. If you’re planning an automation project that requires thoughtful mechanical design, I’d be happy to discuss how an integrated approach might benefit your specific application.
Contact me to explore how your mechanical systems can be optimized for modern automation requirements.